Infolge knapper werdender Flächen und zunehmender Automatisierung denken immer mehr Logistikunternehmen nicht nur weiter, sondern auch höher. Beispiele dafür sind die Hochregallager für Container von Boxbay und für Tiefkühlware bei Nordfrost.
Fotos: SMS Group, Nordfrost, Harry Köster Fotografie
Container mithilfe von Hochregallagertechnik höher zu stapeln, wurde zwar bereits in den 1980er-Jahren versucht. Der Bedarf hielt sich in der Vergangenheit jedoch in Grenzen: „Es gab damals noch genug Flächen an den Hafenterminals“, so Dobner. Das habe sich nun geändert, vor allem in Bezug auf den Handling Aufwand beim Umstapeln, den Stromverbrauch, den Personaleinsatz und den Zeitaufwand.
„Nur ganz wenige Unternehmen auf der Welt kennen sich so gut wie wir mit dem Handling großer und schwerer Lasten aus“, unterstreicht Katja Windt, Chief Digital Officer (CDO) bei der SMS Group. So wurden unter anderem spezielle Hochregallager für bis zu 40 Tonnen schwere Metallcoils entwickelt. In bis zu 50 Meter hohen Regalen können diese rund um die Uhr automatisiert ein- und ausgelagert werden.
Umfangreiche Tests in Dubai waren erfolgreich
Nach vielen Entwürfen folgten die Gründung des gemeinsamen Joint Ventures namens Boxbay im Jahre 2018 und der Baubeginn der Proof-of- Concept(POC)-Testanlage im Hafen Dschabal Ali in Dubai im Sommer 2019. Nach 18 Monaten Bauzeit wurde diese 2021 in Betrieb genommen, und bis heute hat man unter realistischen Betriebsbedingungen über 200.000 Containerbewegungen durchgeführt. Die angestrebte Funktionalität, Leistung und Produktivität der Anlage sowie die Marktreife konnten in dieser Zeit belegt werden.
Nun steht der nächste große Schritt an: Als weltweit erste kommerzielle Anwendung wird im südkoreanischen Hafen Busan ebenfalls ein Container-Hochregallager gebaut. Pusan Newport Corporation (PNC) ist eine DP-World-Tochter, und das Signal in puncto Automatisierung in die Branche ist somit groß. Denn gerade auf den Containerstellflächen besteht noch erheblicher Nachholbedarf.
„Die Logistik wird durch Boxbay vereinfacht, da sich alle Boxen im direkten Zugriff befinden und die Vorhersage der Verfügbarkeit präzise möglich ist“, erläutert Dobner. Bei der klassischen Stapelung kommen zwar komplexe Lagerverwaltungsalgorithmen zum Einsatz, um geschickt zu stapeln und zu entstapeln. Oft ist dennoch der Lkw oder Straddle-Carrier schon da, wenn der RTG (gummibereifter Containerstapelkran) oder RMG (schienengeführter Portalkran) aber noch mit Umstapeln beschäftigt ist.
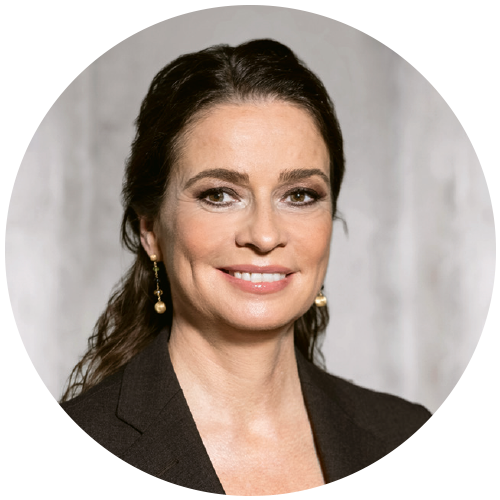
„Das Projekt in Korea war
der Durchbruch.“
Katja Windt, CDO bei der SMS Group
„Das Projekt in Korea war der Durchbruch“, freut sich Windt. „Zurzeit befinden wir uns in 20 bis 30 Gesprächen über weitere Anwendungen“, ergänzt Dobner. „Besonders eignet sich ein solches Hochregallagersystem für Häfen mit einem Umschlag ab 500.000 TEU pro Jahr – und vor allem besonders dann, wenn Platzmangel für Erweiterung herrscht.“
Hochregallager für palettierte Tiefkühllebensmittel
Auch das Unternehmen Nordfrost, das palettierte Tiefkühllebensmittel von Gemüse über Fisch, Fleisch, Backwaren und Convenience-Produkte bis hin zu Eiskrem lagert und distribuiert, setzt seit 2020 in Herne und seit 2021 am Seehafen-Terminal im Containerhafen Wilhelmshaven auf vollautomatische Hochregallager. Mithilfe von Automatisierungstechnik will der Logistiker die Anforderungen der Kunden in der Tiefkühllogistik insbesondere in Bezug auf Qualität und Flexibilität erfüllen.
Bereits die Lkw können am Nordfrost Seehafen-Terminal vollautomatisch be- und entladen werden. „Das ist im Dienstleistungsbereich ein Novum“, betont Britta Bartels, geschäftsführende Gesellschafterin bei Nordfrost. „Dadurch werden die Logistikprozesse beschleunigt, die Ladekapazität der Fahrzeuge wird effizient genutzt, und es werden weniger manuelle Tätigkeiten unter Tiefkühlbedingungen durchgeführt.“
Die Vollautomatisierung in den Hochregallagern umfasst aber auch wichtige Prozessschritte wie die Verbringung der Ware auf Paletten über die Palettenfördertechnik vom Wareneingang in den Lagerbereich. Ebenso erfolgen die Einlagerung in die Regale durch Regalbediengeräte sowie die spätere Auslagerung für Kundenaufträge und die Verbringung in den Warenausgang zur Verladung vollautomatisch.
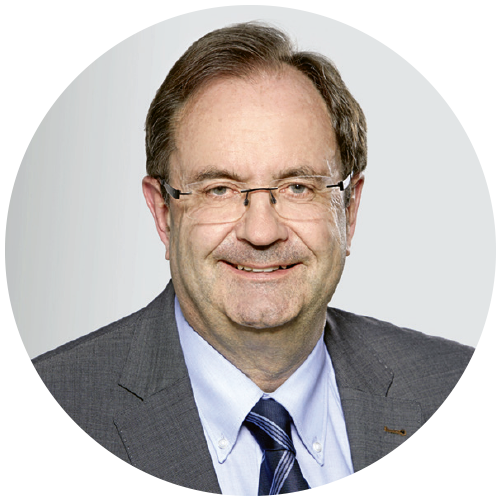
„Mit unserem Hochregallagersystem können 3.000 statt 500 TEU auf einem Hektar stehen.“
Mathias Dobner, CEO bei Boxbay
Automatische Kommissionierung von bis zu 125 Mischpaletten
„Dem vollautomatischen Hochregallager in Herne ist sogar eine automatische Kommissionierung angeschlossen, die sich durch eine sehr hohe Leistungsfähigkeit in Bezug auf Geschwindigkeit und Qualität der Aufgabenerfüllung auszeichnet“, so Bartels. Ein Beispiel: Bis zu 125 Mischpaletten pro Stunde können gemäß der Bestellung der Empfänger – auch bei umfangreichen und wechselnden Sortimenten – automatisch kommissioniert werden.
Dafür ermöglichen es in den automatischen Lagerbereichen in Herne verschiedene Arten von Fördertechniken, sowohl Paletten als auch einzelne Kartons zu bewegen. Um die Kartons von der Palette abzupacken, steht eine automatische Depalletieranlage zur Verfügung. Im sogenannten Shuttlelager werden die vereinzelten Kartons zwischengelagert, ehe sie für den jeweiligen Kommissionierauftrag abgerufen werden.
Besondere Flexibilität bietet aus Sicht von Nordfrost die an beiden Standorten gewählte Kombination von automatischen und manuellen Prozessen, um ganz verschiedene Arten von Ware im Lager und in der Kommissionierung zu handeln. „Das ist wichtig, damit wir als Logistikdienstleister unterschiedlichste Kundenanforderungen bedienen können. Denn die vollautomatischen Prozesse eignen sich nur für Waren und Ladungsträger, die den technischen Anforderungen zum Beispiel an die Palettenmaße entsprechen“, so Bartels.
Auch wenn die derzeit im Bau beziehungsweise in Planung befindlichen Bauprojekte in Wilhelmshaven, Wesel und Bremerhaven keine vollautomatischen Hochregallager enthalten, steht für die geschäftsführende Gesellschafterin bereits fest: „Automatisierung und Digitalisierung bestimmen zunehmend die Zukunft der Logistik.“ (cb)
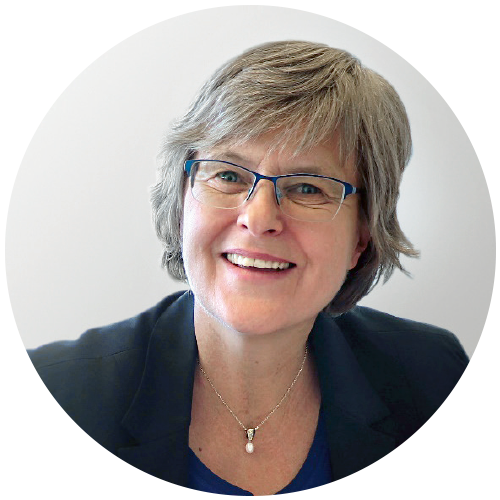
„Automatisierung und Digitalisierung bestimmen zunehmend die Zukunft
der Logistik.“
Britta Bartels, geschäftsführende
Gesellschafterin bei Nordfrost