With the amount of space available dwindling and automation on the rise, more and more logistics companies are not only thinking ahead, but are also thinking upwards. Examples include the high-bay storage systems for BOXBAY containers and for NORDFROST frozen foods.
Credits: SMS Group, Nordfrost, Harry Köster Fotografie
An attempt was made in the 1980s to stack containers even higher using high-bay storage technology, but demand was limited in the past. “Back then, there was still enough space at the port terminals,” stated Dobner. That has since changed, he added, largely in terms of restacking activities, electricity consumption and staff and time requirements.
“Very few companies around the world are as well acquainted as we are with handling large and heavy loads,” emphasised Katja Windt, Chief Digital Officer (CDO) of the SMS Group. Featuring shelves up to 50 metres in height, special automated high-bay storage systems have been developed to accommodate up to 40 tonnes of heavy metal coils, which can be stored and retrieved 24 hours a day.
Extensive testing in Dubai was successful
Many drafts later, the BOXBAY joint venture was founded in 2018, and construction of the proof-of-concept (POC) test system at the Port of Jebel Ali in Dubai kicked off in summer 2019. After a construction period of 18 months, the system began operating in 2021, with more than 200,000 container movements conducted under realistic operating conditions since then. During this time, the testing demonstrated the desired function, performance and productivity and confirmed that the system was ready for the market.
And now it is time for the next major step: a high-bay storage system for containers is now under construction at the Port of Busan in South Korea, representing the world’s first commercial application. The Pusan Newport Corporation (PNC) is a subsidiary of DP World, making the automation statement all the bigger in the sector. That is because there is a lot of catching up to do particularly in container spaces.
“BOXBAY simplifies logistics, as all the boxes are directly accessible, and availability can be predicted with precision,” explained Dobner. Whilst traditional stacking requires complex warehouse management algorithms to ensure intelligent stacking and unstacking, the lorry or straddle carrier is often already there when the rubber-tyred gantry (RTG) or rail-mounted gantry (RMG) crane is still in the process of restacking.
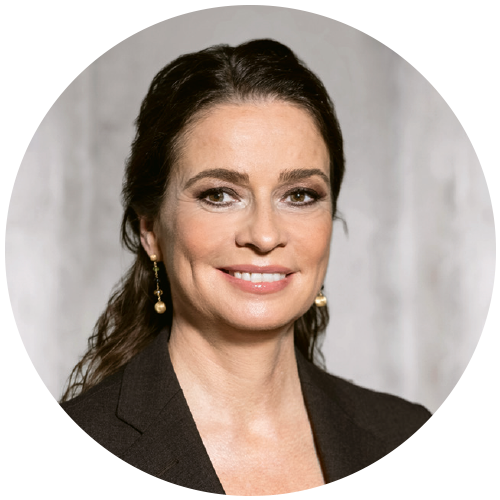
“The project in South Korea
was the breakthrough.”
Katja Windt, CDO of the SMS Group
“The project in South Korea was the breakthrough,” said Windt with delight. “We’re currently involved in 20 to 30 conversations about additional applications,” added Dobner. “This type of high-bay storage system is ideal for ports that handle 500,000 TEU or more a year – especially if there’s limited space for expansion.”
High-bay storage systems for palletised frozen foods
NORDFROST, the company which warehouses and distributes a variety of palletised frozen foods, from vegetables, fish and meat to baked goods, convenience products and ice cream, has also been using fully automated high-bay storage systems in Herne since 2020 and at Container Terminal Wilhelmshaven since 2021. Using automation technology, the logistics company plans to fulfil customers’ requirements in frozen food logistics, with a particular focus on quality and flexibility.
The process of loading and unloading lorries at the NORDFROST Seaport Terminal is already fully automated. “That’s something new in the services sector,” emphasised Britta Bartels, Managing Director of NORDFROST. “This will accelerate logistics processes, ensure efficient use of vehicle loading capacities and reduce the amount of manual work required in freezer spaces.”
But full automation in high-bay storage systems also extends to important process steps such as transporting palletised goods from incoming goods to the warehouse using pallet conveyor technology.
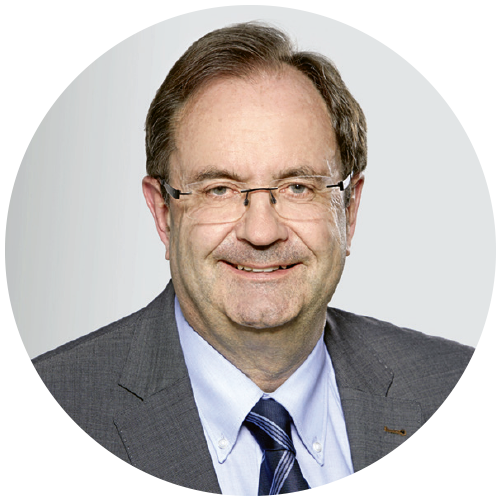
“Our high-bay storage system can accommodate 3,000 rather than 500 TEU on one hectare.”
Mathias Dobner, CEO of BOXBAY
Automated packing of up to 125 mixed pallets
“There’s even an automated picking system connected to the fully automated high-bay storage system in Herne that fulfils its tasks at exceptional speed and with very high quality,” continued Bartels. For example, up to 125 mixed pallets can be packed automatically per hour based on recipients’ orders, even with an extensive and alternating range.
A variety of conveyor technology types make it possible to move pallets and individual boxes in the automated warehouse areas in Herne. There is an automated depalletiser system available for removing boxes from pallets. Individual boxes are temporarily stored in the so-called shuttle warehouse until they are accessed for order picking.
The combination of automated and manual processes selected at both locations provides NORDFROST with extraordinary flexibility, allowing the company to handle an extensive range of goods in the warehouse and during the picking process. “That’s important because it allows us as a logistics service provider to fulfil a whole host of customer requirements. The fully automated processes are only suitable for goods and load carriers that fulfil technical requirements in terms of pallet dimensions, for example,” stated Bartels.
Even if the building projects currently under construction or in the planning phase in Wilhelmshaven, Wesel and Bremerhaven do not contain fully automated high-bay storage systems, the managing partner is sure of one thing: “Automation and digitalisation are increasingly shaping the future of logistics.” (cb)
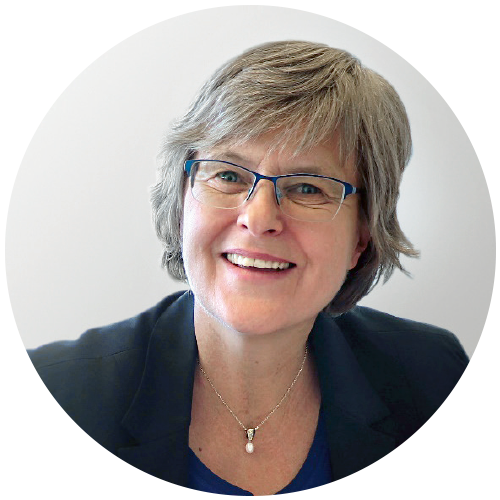
“Automation and digitalisation are increasingly
shaping the future of logistics.”
Britta Bartels, Managing Partner,
NORDFROST