Cuxport got ready for Brexit in good time. An essential part was played by the extension and adjustment to the existing IT systems. This enabled the port services provider to score with the car manufacturer BMW.
Although it was unclear for a long time whether, and if so, when and under what conditions trading would continue between the UK and Germany in the future, Cuxport decided to prepare for all eventualities at an early stage. “We didn’t know exactly what to do when, but it was better not to activate an interface if necessary rather than to have none at all,” explained Dominic Küchler, Head of IT at Cuxport. Back in 2017, after the then British Prime Minister Theresa May formally launched the exit negotiations at the end of March, initial considerations were launched as to how to shape the processes in the future and what adjustments had to be made to IT.
Manual efforts would have been too much
The challenge here was the new customs processes to be introduced require specific data and knowledge, are labour-intensive and liable to errors if done manually. “We quickly realised that the paperwork at border crossings needed to be supported digitally,” emphasised Küchler. “With around 4,000 to 6,000 vehicles and seven crossings per week to the UK, manual customs clearance was not on the cards. After all, in spite of the additional paperwork, our services should continue to comprise a quick approval and/or same-day shipment, even with short standing times of only 30 minutes in some cases.”
To meet these requirements, we basically had to makethree necessary adjustments for the successful integration of automated customs processes. Firstly, the current system had to be extended to include functionalities and status information for the administration of customs references; secondly, an interface to the Dakosy customs software, the software company that specialises in transport and shipping; thirdly, an adjustment to the interfaces from 2011 which are used with shipowners and OEMs (Original Equipment Manufacturer) for the handling of new vehicles. “After preparing well in cooperation with our software suppliers, we have installed the necessary interfaces in our operational system,” reported Küchler. “This enabled the necessary, digitally processed dialogue with the Dakosy customs software and guarantees, at the same time, the security required for the processes.”
Extensive coordination/agreement needs
A team spent roughly six months under the leadership of Küchler in implementing the processes. “The biggest challenge was bringing together the different participants involved, spanning shipowners, ships, terminals and local authorities, with their respective and not always identical requirements for the system,” continued the IT manager. “The name of the game was agreeing on points and coordination work.” Only in this way was it possible to create common ground for the different data formats, which is easier to build and service.
When BMW, which is one of our key clients, put out a tender, Cuxport was already well prepared, in order to be able to depict future processes, not only in terms of operational aspects but also from an IT perspective, in addition to keeping logistic processes to a minimum. This also convinced the car manufacturer which, besides the advantage of daily departures and arrivals as well as the fast and reliable preparation of border traffic with the UK – fiscally now treated as a third country, decided to import the high-voltage mini into Europe mainly via Cuxhaven. Consequently, Cuxhaven and Bremerhaven have been the only transshipment ports for BMW in Europe since early 2020; Cuxhaven handles the import and export of cars to and from the United Kingdom whilst Bremerhaven takes care of customs clearance for cars destined for South Africa and USA.
“Customs clearance went well right from the word go,” said a very happy Küchler. Import and export went as planned right from the very first departures. “The automated exemption has been working more than 99 per cent of the time – you can’t wish for better than that,” emphasised the IT manager. The direct link also ensures that no time is lost during import customs clearance, which would lead to a penalty payment.
Business increased as early as March, and no problems were encountered in April. Furthermore, we are confident that we can expand business even further in the future. The port services provider is ready to add to the two million BMW cars shipped up until 2019 – not only on short crossings but deep sea shipments too. After all, it is obvious what Brexit has changed: third-country business has now become the most important business sector for Cuxport. (cb)
Possible integration of customs procedures in your supply chain
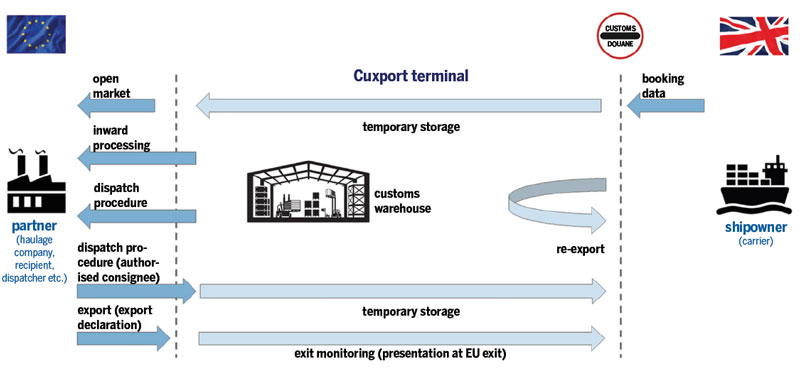
Facts
Cuxport
Joint venture: Rhenus (74.9 per cent)
and HHLA 25.1 per cent
Location: Cuxhaven
Established: 1997
Area of business: Operation of a multi-functional transshipment terminal in Cuxhaven’s deep water port
Employees: 220

“We quickly realised that the paperwork at border crossings needed to be supported digitally.”
Dominic Küchler, Head of IT at Cuxport